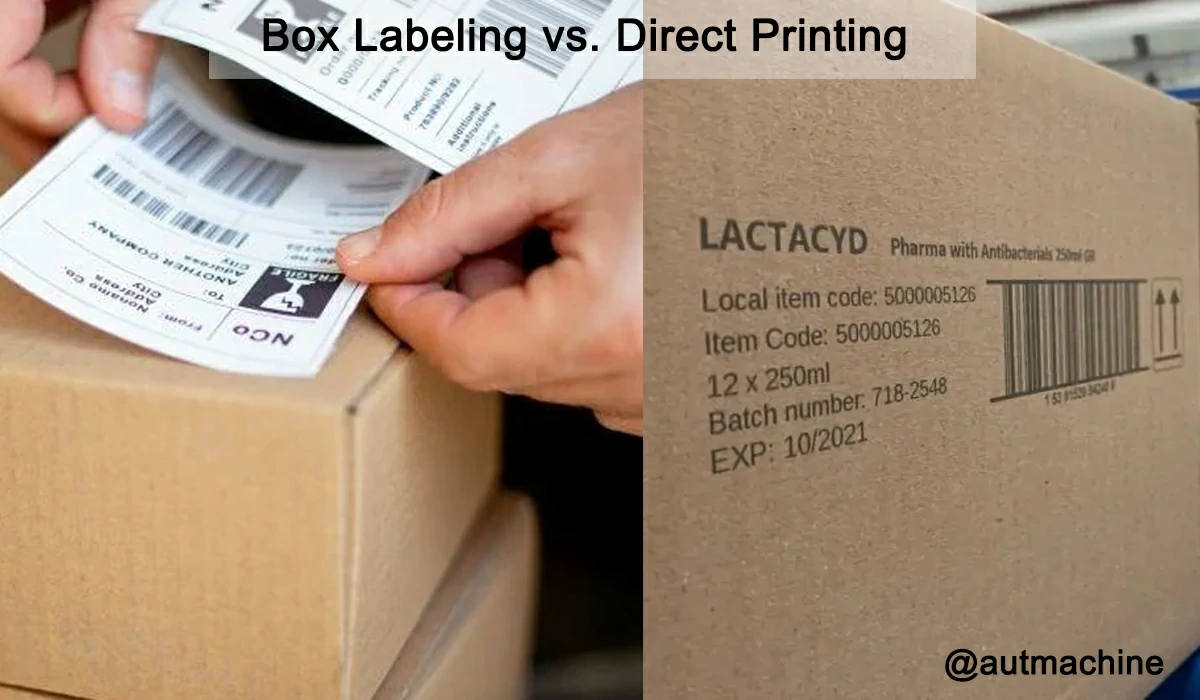
In logistics, cartons are very suitable for the safe transportation of goods. As products traverse complex supply chains, the method used to label and mark boxes is critical. This decision can impact everything from shipping accuracy and branding to recycling capabilities and long-term cost efficiency. For manufacturers and businesses, the choice between box labelling and direct printing is often not clear-cut.
In this comprehensive guide, we will examine the advantages, disadvantages, and key differences between box labelling and direct printing, helping you choose the right method for your needs.
Understanding Box Labelling
Box labelling involves applying a printed sticker or label onto the surface of a carton or package, a process commonly facilitated by label applicators or labeling machines. These machines use various techniques, including thermal transfer printing, to achieve high resolution and clear legibility.

Labels can be made of various materials, such as paper or plastic, and typically feature printed text, graphics, barcodes, or QR codes, including automated systems or manual application. This method is widely adopted across industries, particularly in retail and logistics, shipping, and inventory management.
Advantages of Box Labelling
- Versatility: Labels can be applied from almost any angle, including the sides, top, and even around corners. This flexibility is especially useful when dealing with boxes of varying sizes and shapes.
- High-Resolution Printing: The print quality on labels is typically superior, offering high clarity for barcodes, serial numbers, and graphics. Thermal transfer printers, for instance, provide exceptional print resolution, often adhering to industry standards such as ANSI Code Grade A.
- Compensation for Surface Irregularities: Labels can conform to the uneven surfaces of corrugated cardboard, ensuring legible barcodes and text even on rough or bumpy surfaces.
Challenges of Box Labelling
- Cost of Consumables: The price of labels and associated materials (e.g., thermal ribbons) can add up over time, especially in high-volume operations.
- Labor and Handling: The process of applying labels can be labor-intensive if done manually, and even automated systems require maintenance and adjustments.
- Environmental Impact: Labels are typically made from non-recyclable materials like adhesives and synthetic papers, which can affect the recyclability of the entire package.
Understanding Box Direct Printing
Direct printing refers to the application of print directly onto the surface of the box or packaging, without the use of labels. This method involves using specialized inkjet printers or large-character printers, typically using high-resolution print heads.

Advantages of Direct Printing
- Lower Operating Costs: Direct printing typically incurs fewer ongoing consumable costs compared to labelling. Ink cartridges, for example, are usually less expensive than labels and thermal ribbons.
- Speed and Efficiency: Direct printing can achieve much higher printing speeds than labelling, making it ideal for high-volume production lines. Some systems can print at speeds up to 1,000 mm/s, compared to the typical 400 mm/s of label applicators.
- Larger Print Area: With direct printing, the printable area is considerably larger, with some systems offering print heights up to 800mm, which can be advantageous for larger cartons or complex designs.
- Sustainability: Since there is no need for labels or adhesives, direct printing can be more environmentally friendly, as it avoids the use of non-recyclable materials. Boxes printed directly can still be recycled without contamination from adhesives or label remnants.
Challenges of Direct Printing
- Print Quality Variability: The print quality on cardboard may be slightly lower due to the absorbent nature of the material. While inkjet printers can achieve high resolution, the print quality can vary based on the cardboard’s color, texture, and absorbency.
- Limited Surface Compatibility: Direct printing works best on relatively smooth and absorbent surfaces. While it can print on corrugated cardboard, the finish may not be as sharp as that of a label.
- Fixed Printhead Position: Unlike labelling systems, which offer more flexibility in terms of print positioning, direct printing requires the printhead to be placed close to the surface. This limits the angles and positions from which printing can occur.
Box Labeling vs. Direct Printing in Comparison
To better understand which method may be more suitable for your business, here’s a side-by-side comparison of box labelling and direct printing across several important factors:
Factor | Box Labelling | Direct Printing |
---|---|---|
Print Quality | High-quality print with thermal transfer, ideal for barcodes. | Ink quality may be affected by cardboard absorbency, leading to less sharp prints. |
Printing Speed | 400 mm/sec | 1,000 mm/sec |
Investment Costs | Comparable to direct printing, with automated labeling equipment. | Similar investment, focusing on inkjet printers and setup. |
Operating Costs | Higher due to costs of labels, ribbons, and adhesives. | Lower, as only ink is needed, no labels or ribbons. |
Print of Text, Images, Graphics, and Codes | Can print text, graphics, and barcodes accurately. | Capable of printing text, images, and codes, but quality may vary. |
Scannability | Excellent, especially for barcodes on white labels, ideal for logistics. | Reduced on brown cardboard, as ink may blur and affect scannability. |
Maximum Resolution | 600 dpi (Thermal Transfer Printing) | 200 dpi (Inkjet Printing) |
Format Change | Cannot change label size during the process; requires reprinting. | Can adjust print size dynamically during printing. |
Print Position | Above, side, below | Above, side |
Adjustability of Labeling Plate / Printhead | Highly adjustable, allowing corner wraps and variable angles. | Static, must be placed close to the surface, with no angle adjustments. |
Maximum Distance to the Carton | Large, due to extendable dispensers or blow-off technology. | Small, as the printhead must be positioned very close to the surface. |
When to Choose Box Labelling
Box labelling is an ideal solution when the priority is high-quality print resolution, especially for applications requiring clear barcodes and product information. This method is particularly well-suited for industries that demand high print clarity and strict compliance with international standards, such as retail and logistics. Additionally, if the packaging involves variable sizes and shapes, labelling offers the versatility needed to adapt to different package dimensions and surfaces.
When to Choose Direct Printing
Direct printing is a better option when speed, cost-efficiency, and sustainability are top priorities. It is perfect for high-volume production environments where the ability to print large areas at a fast rate is crucial. If your business needs to mark a lot of boxes quickly and at a lower cost, direct printing can be the ideal solution. Furthermore, for companies looking to minimize their environmental impact, direct printing’s recyclability offers a more sustainable alternative to traditional labelling.
Conclusion
Ultimately, the right choice will depend on factors like print quality requirements, production speed, sustainability goals, and packaging type. Understanding these factors and assessing the specific needs of your business will help you make a more informed decision.
Would you like to dive deeper into the specifics of either method or discuss how to implement these techniques in your packaging process? Get in touch with our experts (jinlian@autmachine.com, penny@autmachine.com) to explore the best solutions tailored to your needs.
At AUTmachine, a leading labeling machine manufacturer based in China, we offer both fully automatic labeling machine and semi-automatic labeling machines that can be seamlessly integrated into your production line—whether you need labeling or inkjet printing for your boxes. Let us help you find the best solution for your business’s needs!
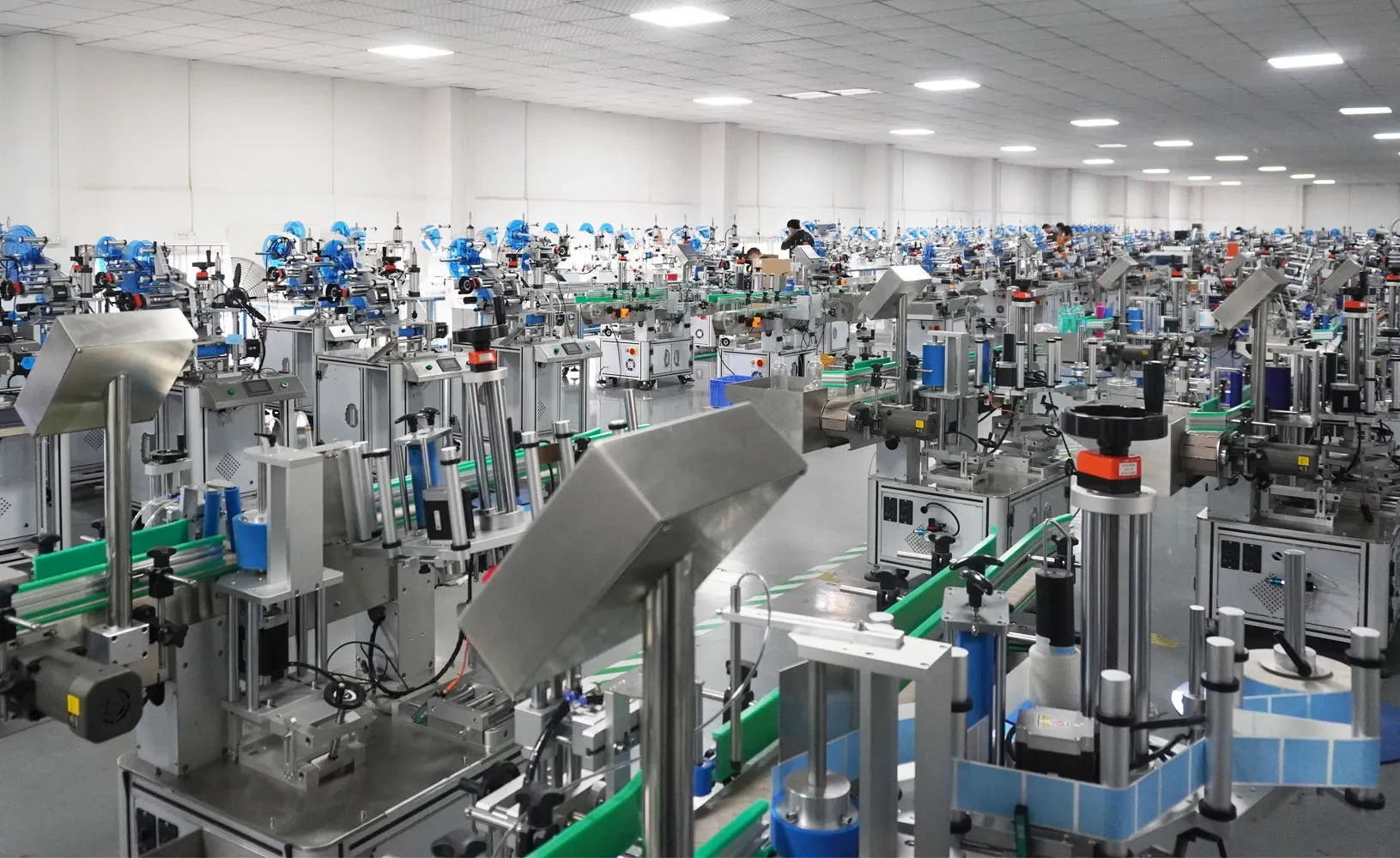
Get your free demo now!
FAQ
Labelling involves applying a printed label onto a cardboard box, while direct printing involves printing information directly onto the surface of the box itself using inkjet technology.
While direct printing can handle text, logos, and simple barcodes, it may not be ideal for intricate designs or multi-color graphics. Labelling provides more flexibility for detailed designs, gradients, or photographic-quality images.
Consider factors like production volume, budget, sustainability goals, print quality requirements, and flexibility in design. If you need high-quality prints and flexibility, labelling is a better choice, but for faster, more cost-effective solutions, direct printing may be ideal.